Z filozofii Lean wynika jednoznacznie, że zapasy surowca mają być na minimalnym poziomie lub ma ich nie być wcale. Coś, co ma wartość finansową, jest stratą. Im mniejsze stany magazynowe posiadasz, tym mniejsze straty ponosisz. Czego jeszcze JIT i Lean nie lubią? Nie lubią zbędnej pracy. Wszelkie przemieszczanie towaru miedzy halą magazynową a halą produkcyjną to kolejne marnotrawstwo, czyli strata czasu i pieniędzy. W JIT zarówno stany magazynowe, jak i praca nie są rozumiane jako czynnik wnoszący wartość dodaną, a traktowane są jako koszty, z którymi trzeba walczyć i dążyć do ich minimalizacji. Filozofia JIT próbuje minimalizować marnotrawstwo związane z materiałami i zbędnymi czynnościami na wiele sposobów.
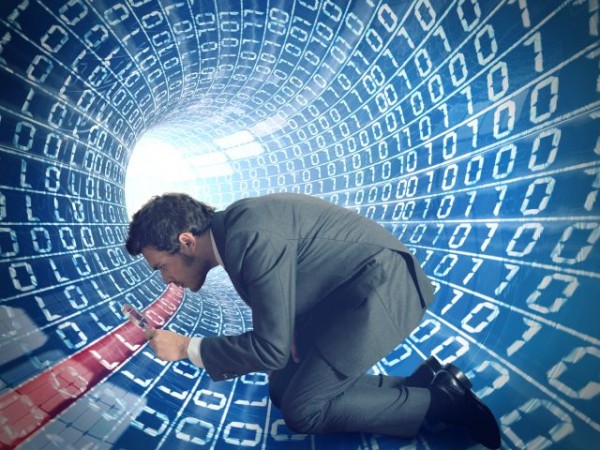
Pierwszym krokiem, jaki powinniśmy podjąć w celu kontroli przepływu surowca, jest przeanalizowanie planów produkcyjnych. Należy się zastanowić, czy dane zlecenia nią są zbyt szybko rozpoczynane i nie będą oczekiwały za długo w magazynie na wysyłkę do klienta. Powinniśmy też przemyśleć, czy dane zlecenie nie posiada zbyt dużej partii i nie wygeneruje nam nadprodukcji, którą i tak będziemy musieli zmagazynować. Oczywiście jest to powodem odwiecznego konfliktu między próbą utrzymania pewnego zapasu gwarantującego ciągłość produkcji a minimalizacją bieżących zapasów. Takie zachowanie dotyczy magazynu surowców, półproduktów i produktów gotowych. Większość firm chce dążyć do tego, aby produkować jedynie takie ilości, jakie zamówili klienci. Można planować też tak, aby w planie produkcyjnym były produkowane te wyroby, które mogą zużywać część tych samych surowców w tym samym czasie, na różnych maszynach. Zminimalizuje to wszelkie ruchy surowców i towarów między magazynem a halą produkcyjną, a w razie wystąpienia awarii będzie można użyć tych surowców do innego zlecenia.
Kolejny problem to dostarczanie na halę produkcyjną zbyt dużej ilości surowca w stosunku do planowanej produkcji, czyli tworzenie miejscowego zapasu. Warto wypracować taki system, aby nigdy na hali nie było zgromadzone zbyt dużo surowców, ale należy również pamiętać, aby nie było ich zbyt mało, ponieważ może to powodować przerwy w produkcji, co wygeneruje dodatkowe koszty. Najlepszym rozwiązaniem jest dostarczać surowce na bieżąco, synchronicznie w „optymalnych porcjach”, a nie w dużych ilościach na początku zmiany lub akurat wtedy, gdy magazyny mają wolny czas. Jeżeli starannie zaplanowaliśmy produkcję pod kątem dostaw surowca, to pierwsza część pracy zamiast przez magazyn została już wykonana przez planowanie produkcji. Teraz wystarczy, by magazyn i produkcja podjęły działania, które będą dążyły do zachowania planu. Pierwszym krokiem powinno być ustalenie, co oznacza „optymalna porcja”, czyli należy ustawić wielkości konkretnych typów surowców. Drugi krok to ustalenie pojemności miejsc składowania tych surowców przy obszarze ich zużywania tak, aby utrzymać ciągłość produkcji. Trzecim elementem jest efektywny system monitorowania bieżącego zużycia surowców. Powinien on generować sygnały o konieczności uzupełnienia surowców na hali produkcyjnej, z informacją na kiedy należy uzupełnić lokalizacje na produkcji.
Ostatnim krokiem w procesie optymalnego dostarczania surowców i odbierania produktów gotowych z hal produkcyjnych jest mierzenie kluczowych parametrów, zarówno w logistyce magazynowania, jak i w logistyce produkcji. Należy dokładnie sprawdzać, ile surowca zostało rzeczywiście zużyte, a nie tylko polegać na normach technologicznych i wartościach uśrednionych. Trzeba też mierzyć, na jak długo starcza nam na produkcji konkretna partia i ilość komponentu oraz ile czasu zajmuje nam dostarczenie surowca z magazynu na halę produkcyjną. Kontrolujemy wszystko, co pozwala nam określić optymalne parametry naszych procesów.
O tym, co jest optymalne, powinna decydować matematyka i ekonomia. Dzisiaj często o wielkościach użytych w produkcji decyduje doświadczenie pracowników. Doświadczenie to rzecz cenna, ale powinniśmy zacząć je wspierać danymi statystycznymi, zbieranymi na bieżąco. Ile firm posiada jedynie normatywne BOM-y, dawno lub nigdy nie weryfikowane? Ile firm codziennie dowozi towar na halę produkcyjną i odwozi go z hali tylko dlatego, że tak się przyzwyczaili?
W dzisiejszych czasach w codziennej pracy mogą nas wspierać zaawansowane systemy informatyczne. Często świetne wyniki daje wprowadzenie nawet stosunkowo prostych systemów planowania produkcji, czyli programów typu APS. Do monitorowania i raportowania produkcji oraz zarządzaniem logistyką mamy szereg innych specjalistycznych narzędzi, jak np. MES czy WMS. Największą wydajność da nam jednak dopiero pełna integracja takich specjalistycznych narzędzi, które na bieżąco będą się ze sobą komunikować, ułatwiając tym samym zarządzanie ruchem towarów i surowców na produkcji w taki sposób, aby niezbędne materiały były dostarczane płynnie w momencie ich rzeczywistego zapotrzebowania.
Maciej Wojtkowiak
Quantum Qguar sp. z o. o.
Quantum Qguar sp. z o. o.