Jednym z najbardziej newralgicznych etapów procesu produkcji, w którym zasady Lean odgrywają kluczową rolę dla zapewnienia produktywności, jest koniec linii. Właściwa organizacja tej strefy zapewnia sprawny przepływ i eliminację „wąskich gardeł” na etapie wyjścia wyrobów gotowych z fabryki.
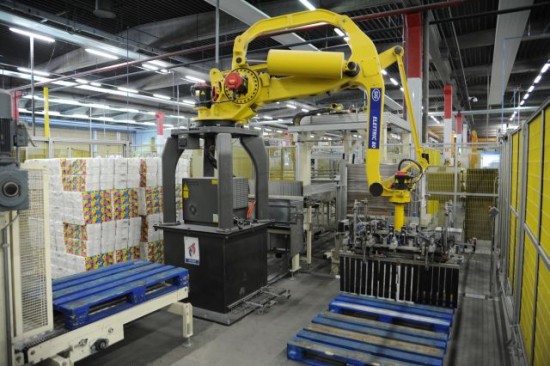
Typowe procesy odbywające się na końcówkach linii produkcyjnej w różnych gałęziach przemysłu to przede wszystkim sztaplowanie, pakowanie, paletyzacja, owijanie, transport. Są to obecnie jedne z najczęściej wdrażanych aplikacji na rynku. Wpływ na to ma rozwój zakładów produkcyjnych, zwiększony wolumen produkcji oraz silniejsza konkurencja na rynku. Naturalnym sposobem powiększenia przychodów i zysków przedsiębiorstwa produkcyjnego jest wzrost sprzedaży produktów. Zdaniem Wojciecha Stachelka z firmy AB Industry, specjalizującej się w projektowaniu i wdrażaniu linii produkcyjnych, planując optymalizację procesów końcówki linii należy zatem uwzględnić czynniki takie, jak:
- Aktualna wielkość produkcji i planowana przez minimum 3 lata;
- Rodzaj opakowania, wielkość, estetyka, szybkość składania kartonu;
- Sposób ułożenia produktów w opakowaniu;
- Sposób zamykania kartonów i oklejanie;
- Sposób układania opakowań na palecie;
- Elastyczność na promocje marketingowe: zmiana opakowania, zmiana wielkości produktu, pakowanie po 2 lub 3 sztuki itp.;
- Różnorodność produkowanego asortymentu i skupienie się na produkcji wielkoseryjnej, gdzie automatyzacja procesu poprawi jakość, efektywność i powtarzalność produkcji.
Z kolei na kwestiach związanych z przestrzenną organizacją strefy końca linii i wydajnością rozwiązania koncentruje się Jędrzej Kowalczyk, Sales Manager w firmie FANUC Robotics Polska. Sugeruje on, by zwrócić uwagę na dostępność miejsca (należy przygotować precyzyjny projekt stanowiska zautomatyzowanego) oraz wydajność urządzenia pod kątem obecnych i przyszłych planów produkcyjnych linii. Istotną kwestią jest możliwość łatwego dopasowania do zmiany gamy produktów, a także niezawodność urządzenia i rozwinięta diagnostyka oraz profesjonalny serwis, w celu uniknięcia nieplanowanych postojów, aby końcem linii nie blokować całej produkcji.
Podstawowymi czynnikami są: rodzaj produkcji, rodzaj produktu oraz parametry wydajnościowe. Obecnie rynek charakteryzuje się dużą dynamiką i wymaga od zakładów produkcyjnych elastyczności. W celu zapewnienia łatwiejszego i szybszego podążania za wymogami rynku, warto się zastanowić, czy wybierane urządzenie pozwoli na zmiany asortymentu, wprowadzenie nowych produktów i nowych opakowań.
– Aktualnie większość aplikacji realizowana jest na robotach przemysłowych, które gwarantują najwyższy poziom elastyczności. Dobierając konkretny model robota, należy przyjrzeć się produktowi (masa, gabaryty) oraz parametrom wydajnościowym. Zarówno udźwig robota, jego zasięg, jak i wydajność powinny zostać dobrane tak, aby możliwa była realizacja zadania przy 20-procentowym zapasie – mówi Paweł Handzlik, Specjalista ds. Robotów Przemysłowych w firmie ASTOR. Na etapie wyboru rozwiązania powinno się dokładnie przeanalizować warianty rozwoju i wybrać rozwiązanie o parametrach umożliwiających dalszy rozwój zakładu.
Jak wspomnieliśmy na wstępie, jedną z typowych operacji końca linii produkcyjnej jest pakowanie. W celu dobrania odpowiedniego urządzenia, które umożliwi optymalizację pakowania produktów na końcu linii produkcyjnej, należy zwrócić uwagę przede wszystkim na rodzaj opakowania jednostkowego oraz na typ opakowania zbiorczego. – Gdy znamy już te dane, w kolejnym etapie należy określić konfigurację, w jakiej będzie grupowany produkt i prędkość jego podawania. Na samym końcu należy ustalić sposób i orientację transportu gotowego kartonu ze zgrupowanym produktem do stacji paletyzacji – tłumaczy Radosław Sakowski z firmy Radpak.
Jak wspomnieliśmy na wstępie, jedną z typowych operacji końca linii produkcyjnej jest pakowanie. W celu dobrania odpowiedniego urządzenia, które umożliwi optymalizację pakowania produktów na końcu linii produkcyjnej, należy zwrócić uwagę przede wszystkim na rodzaj opakowania jednostkowego oraz na typ opakowania zbiorczego. – Gdy znamy już te dane, w kolejnym etapie należy określić konfigurację, w jakiej będzie grupowany produkt i prędkość jego podawania. Na samym końcu należy ustalić sposób i orientację transportu gotowego kartonu ze zgrupowanym produktem do stacji paletyzacji – tłumaczy Radosław Sakowski z firmy Radpak.
Oprócz aspektu typowo ekonomicznego, celem automatyzacji procesów na końcu linii często jest poprawa jakości bądź zwiększenie powtarzalności w procesach pakowania lub paletyzacji. – Innym powodem może być poprawa bezpieczeństwa, chociażby poprzez wyeliminowanie niepotrzebnego ruchu wózków widłowych. Wychodzi więc na to, że zanim zaczniemy zastanawiać się nad doborem systemów automatyzujących końcówkę linii, musimy zdecydować, w jakim stopniu chcemy ją automatyzować. Nierzadko automatyzowanie specyficznej części procesu jest ekonomicznie nieuzasadnione – mówi Filip Rogiewicz, Członek Zarządu PROTiM.
Zdaniem naszego rozmówcy, na etapie analizy przedwdrożeniowej należy prześledzić proces i wytypować w nim:
– operacje nieergonomiczne i uciążliwe dla człowieka;
– procesy czasochłonne, angażujące dużą liczbę osób;
– procesy powtarzalne, które łatwo zastąpić automatami;
– procesy niebezpieczne dla człowieka.
– operacje nieergonomiczne i uciążliwe dla człowieka;
– procesy czasochłonne, angażujące dużą liczbę osób;
– procesy powtarzalne, które łatwo zastąpić automatami;
– procesy niebezpieczne dla człowieka.
Powyższa analiza pozwoli ocenić, które zakresy procesu powinny zostać zautomatyzowane. Kolejnym krokiem jest analiza i ocena możliwości automatyzowania wybranych operacji. Aspekt ten najlepiej badać przy wsparciu dostawców zautomatyzowanych systemów końcówek linii.
Ekonomia zakupu
Konieczność optymalizacji procesów na końcu linii produkcyjnej w celu eliminacji „wąskich gardeł” jest oczywistością. Automatyzacja tego obszaru wydaje się doskonałym wyjściem. Należy jednak rozważnie podejść do kwestii inwestycji w konkretne rozwiązanie, analizując potencjalny zwrot z inwestycji.
W opinii Jędrzeja Kowalczyka z FANUC Robotics przede wszystkim należy określić potrzeby klienta i priorytety, jakie są związane z inwestycją – czasami może to być zwiększenie wydajności, czasami poprawa jakości czy stabilność produkcji. W oparciu o cel, jaki ma zostać zrealizowany, należy opracować właściwą koncepcję stanowiska z wykorzystaniem odpowiednich urządzeń. – Na zwrot z inwestycji mają wpływ nie tylko czynniki, które bezpośrednio można wykazać w raportach finansowych, jak zwiększenie wydajności czy zminimalizowanie kosztów związanych z utrzymaniem linii, ale także czynniki, które doceniane są po upływie pewnego czasu, jak: stabilność produkcji, zwiększenie bezpieczeństwa w zakładzie i poprawa jakości, która przyczynia się do zmniejszenia liczby wadliwych partii produkcyjnych – wyjaśnia ekspert FANUC Robotics. Powyższe czynniki mają wpływ nie tylko na określenie czasu zwrotu z inwestycji, ale również na polepszenie współpracy z kontrahentami. Można pewniej planować produkcję, przy okazji minimalizując czy wręcz wykluczając ryzyko dostarczenia wadliwych produktów. Przekłada się to bezpośrednio na unikanie kar wynikających z umów z kontrahentami.
Biorąc pod uwagę np. pakowanie, jednym z najważniejszych czynników jest ilość pracowników przydzielonych do jednego zadania na końcowym etapie linii produkcyjnej. Dzięki zastosowaniu automatycznego systemu pakowania zbiorczego możliwe jest przede wszystkim zastąpienie pracy ludzkiej pracą maszynową. Należy również wziąć pod uwagę możliwość zwiększenia wydajności całej linii produkcyjnej, której wcześniejsze „wąskie gardło” jest dzięki maszynie pakującej w pełni zgranym mechanizmem całego systemu. – Na koniec argument dotyczący ergonomii pracy, która na tym etapie produkcji jest rutynowa i monotonna, co przekłada się na częstsze popełnianie błędów oraz brak zaangażowania pracowników. W przypadku zastosowania maszyn do ich realizacji, unikniemy błędów, zyskamy wyższą wydajność oraz będziemy mogli przenieść pracowników do innych zadań – podpowiada Radosław Sakowski z firmy Radpak.
Istotnym parametrem są koszty. Oczywiście muszą się one mieścić w budżecie i powinny być optymalizowane pod względem efektów i zysków. Pamiętając, że koszty skorelowane są z tym, co otrzymujemy, należy zwrócić uwagę, aby wybrać rozwiązanie niekoniecznie najtańsze, ale optymalne. Precyzyjne zdefiniowanie tego, czego oczekujemy od aplikacji, pozwoli na wybór optymalnego rozwiązania zarówno funkcjonalnie, jak i kosztowo. – Na podstawie zestawienia oczekiwań i funkcjonalności można określić realny budżet. Znając budżet i funkcjonalność (a więc i oczekiwane efekty, jakie przyniesie inwestycja), należy wykonać analizę zwrotu z inwestycji. Pozwala ona nie tylko sprawdzić, czy inwestycja opłaca się, ale również wybrać wariant, który pozwoli uzyskać optymalne zyski w odniesieniu do ponoszonych kosztów. W takiej analizie należy uwzględnić możliwie wszystkie koszty i zyski. Szczególnie zyski mogą być trudne do lokalizacji i zmierzenia. Warto na tym etapie skontaktować się konsultantami z firmy dostarczającej dane rozwiązanie i wspólnie opracować taką analizę – radzi Paweł Handzlik z firmy ASTOR.
Przykładowe rozwiązania
W obszarze rozwiązań stosowanych na końcówkach linii produkcyjnych ASTOR proponuje pięcioosiowy robot do paletyzacji – Kawasaki RD080N. O sukcesie firm produkcyjnych coraz mocniej decyduje elastyczność całego procesu produkcji. Wychodząc naprzeciw potrzebom klienta, firma Kawasaki stworzyła dedykowaną serię robotów, która w obszarze paletyzacji, pakowania i przenoszenia gwarantuje najwyższy poziom elastyczności i dopasowania do wymogów produkcji.
Robot paletyzujący RD080N to model dedykowany do przenoszenia i paletyzacji ładunków o masie do 80 kg, posiadający pięć stopni swobody. Kompaktowe wymiary robota i zasięg do 2,1 m, pozwalają na zastosowanie go w małych przestrzeniach, np. bezpośrednio na linii produkcyjnej. Zastosowanie kontrolera serii E, z nowoczesnym procesorem Intel oraz szybkich napędów dużej mocy pozwoliło zwiększyć prędkość pracy robota. Atrybuty te umożliwiają obsługę nawet kilku linii produkcyjnych przez jednego robota.
Robot paletyzujący RD080N to model dedykowany do przenoszenia i paletyzacji ładunków o masie do 80 kg, posiadający pięć stopni swobody. Kompaktowe wymiary robota i zasięg do 2,1 m, pozwalają na zastosowanie go w małych przestrzeniach, np. bezpośrednio na linii produkcyjnej. Zastosowanie kontrolera serii E, z nowoczesnym procesorem Intel oraz szybkich napędów dużej mocy pozwoliło zwiększyć prędkość pracy robota. Atrybuty te umożliwiają obsługę nawet kilku linii produkcyjnych przez jednego robota.
Niezawodność pracy zapewnia nowoczesna konstrukcja jednostki mechanicznej i pięcioosiowa konstrukcja. Smukła sylwetka i mała podstawa czyni z robota idealną jednostkę do pracy w celach lub ciasnych liniach produkcyjnych.
Robot RD080N, dostarczany jest wraz z nowoczesnym kontrolerem Kawasaki serii E, wyposażonym w oprogramowanie dedykowane do paletyzacji i przenoszenia. W zestawie robot posiada ergonomiczny i przyjazny w użytkowaniu programator ręczny, z kolorowym, dotykowym ekranem o przekątnej 6,4” i dedykowanymi przyciskami umożliwiającymi łatwe i efektywne programowanie. Programator może zostać wykorzystany także jako panel operatora.
Również w ofercie FANUC Robotics potencjalny użytkownik znajdzie roboty paletyzujące przeznaczone do zadań na końcach linii produkcyjnych. Znajdują one zastosowanie praktycznie w każdej branży, gdyż gama robotów paletyzujących odpowiada bardzo szerokim potrzebom rynku zarówno pod względem parametrów technicznych, jak i ekonomicznych. – Roboty dedykowane do tych procesów stosowane są od wielu lat, dzięki czemu ich zastosowania spełniają najbardziej wymagające oczekiwania klientów. Wspomnę tutaj choćby o przelotowej kiści robota, ułatwiającej podłączenie przewodów głowic chwytających czy o umiejscowieniu kontrolera robota pod jednostką mechaniczną, dzięki czemu miejsce zajmowane przez maszyny na linii produkcyjnej jest absolutnie zminimalizowane – mówi Jędrzej Kowalczyk. Poza korzyściami wynikającymi z własnej konstrukcji, roboty FANUC posiadają także możliwość wykorzystania opcji ułatwiających proces programowania, optymalizację pracy robota, użytkowania, aż po diagnozowanie stanu robota.
Kompletny system pakowania zbiorczego proponuje z kolei firma Radpak. Model RKZ-27 pozwala na pełną automatyzację końca linii produkcyjnej. Umożliwia on odbiór różnego rodzaju opakowań jednostkowych, od toreb płaskich/saszetek, toreb stabilo, typu doypack czy też z fałdą boczną, po różnego rodzaju kartoniki, tacki, pojemniki itp. Dzięki nowatorskim rozwiązaniom możliwe jest zgrupowanie produktów jednostkowych w różnych konfiguracjach oraz ich załadunek do 3 rodzajów formowanych kartonów:
1) zawijany – wrapped-around;
2) podstawa z oddzielną pokrywą – tray&hood;
3) podstawa – tray.
Kartony są automatycznie formowane na maszynie oraz, w zależności od typu, mogą być zamykane za pomocą aplikatora kleju lub pokrywą, która również jest formowana automatycznie, a później nakładana za pomocą zintegrowanego manipulatora 2-osiowego. Zastosowanie wydajnych i precyzyjnych serwosilników, synchronizacja wszystkich stacji oraz zaawansowane systemy, jak np. indeksowy przenośnik serwo, pozwalają na uzyskanie wysokich wydajności i odbieranie nawet 100 produktów jednostkowych na minutę.
W projektowaniu i wdrażaniu linii produkcyjnych specjalizuje się również firma AB Industry, która oferuje rozwiązania z zakresu automatyzacji końcówek linii produkcyjnych. – Każda nasza realizacja charakteryzuje się innowacyjnym rozwiązaniem, trwałością i szybkim zwrotem z inwestycji. Nasze aplikacje najczęściej działają w trudnych warunkach pracy: duże ciężary podnoszonych elementów, wysoka wydajność produkcji, powtarzalność ruchów, niska lub wysoka temperatura, hałas i zapylenie – mówi Wojciech Stachelek. Wdrażane przez firmę centra paletyzacji obsługują wysokowydajne linie produkcyjne. Stanowiska do paletyzacji AB Industry wykorzystują roboty przemysłowe, które przenoszą: worki, kartony, butelki, zgrzewki, profile i tafle szkła, a dotychczasowe aplikacje znalazły zastosowanie w przemysłach: spożywczym, kosmetycznym, chemicznym i motoryzacyjnym. Wydajność linii zawsze jest dopasowana do oczekiwań klienta.
Przykładem rozwiązania znajdującego zastosowanie na końcach linii produkcyjnej, które proponuje poznańska firma PROTiM, są automatyczne formierki kartonów i tac (displayów) kartonowych. Maszyny te pozwalają na automatyczne przygotowanie kartonów/tac i podanie ich do stanowisk ręcznego lub automatycznego pakowania. Zalet tego rozwiązania jest co najmniej kilka. Przede wszystkim karton czy taca formowane automatycznie są znacznie tańsze niż analogiczne przewidziane do formowania ręcznego W przypadku ręcznego formowania jest to proces czasochłonny i monotonny, co sprawia, że zwrot inwestycji jest szybki. – Dzięki automatycznej formiarce zyskujemy powtarzalną jakość i wysoką estetykę złożonych kartonów, a także możliwość automatyzowania etapowego, np. pierwszy etap to automatyczne formowanie kartonów, a pakowanie odbywa się ręcznie, kolejny etap to zautomatyzowanie etapu pakowania w uprzednio automatycznie uformowane kartony – mówi Filip Rogiewicz. Wydajność jednej maszyny jest od 3 do 8 razy wyższa niż człowieka (zależnie od typu kartonu/tacy), a urządzenia te znajdują zastosowanie praktycznie we wszystkich branżach, gdzie pojawiają się tekturowe opakowania zbiorcze. Można więc powiedzieć, że w całym obszarze FMCG, jak i wielu innych branżach. Wydajności uzależnione są od zapotrzebowania klienta oraz typu kartonu/tacy i wahają się pomiędzy 11 a 30 kartonów lub tac na minutę.
Przykładem rozwiązania znajdującego zastosowanie na końcach linii produkcyjnej, które proponuje poznańska firma PROTiM, są automatyczne formierki kartonów i tac (displayów) kartonowych. Maszyny te pozwalają na automatyczne przygotowanie kartonów/tac i podanie ich do stanowisk ręcznego lub automatycznego pakowania. Zalet tego rozwiązania jest co najmniej kilka. Przede wszystkim karton czy taca formowane automatycznie są znacznie tańsze niż analogiczne przewidziane do formowania ręcznego W przypadku ręcznego formowania jest to proces czasochłonny i monotonny, co sprawia, że zwrot inwestycji jest szybki. – Dzięki automatycznej formiarce zyskujemy powtarzalną jakość i wysoką estetykę złożonych kartonów, a także możliwość automatyzowania etapowego, np. pierwszy etap to automatyczne formowanie kartonów, a pakowanie odbywa się ręcznie, kolejny etap to zautomatyzowanie etapu pakowania w uprzednio automatycznie uformowane kartony – mówi Filip Rogiewicz. Wydajność jednej maszyny jest od 3 do 8 razy wyższa niż człowieka (zależnie od typu kartonu/tacy), a urządzenia te znajdują zastosowanie praktycznie we wszystkich branżach, gdzie pojawiają się tekturowe opakowania zbiorcze. Można więc powiedzieć, że w całym obszarze FMCG, jak i wielu innych branżach. Wydajności uzależnione są od zapotrzebowania klienta oraz typu kartonu/tacy i wahają się pomiędzy 11 a 30 kartonów lub tac na minutę.
Michał Klecha