Metoda 5S (praktyki 5S) jest to metoda kontroli wizualnej, która przyczynia się do poprawy funkcjonowania w każdej ze sfer działalności przedsiębiorstwa. Zasady w jej ramach mogą być wykorzystane podczas produkcji, w procesach magazynowania, a także w biurze.
Polega ona na stworzeniu, utrzymaniu i ciągłym doskonaleniu stanowiska pracy, tak aby było ono czyste, uporządkowane i odpowiednio zorganizowane. Zakłada pracę według ustalonych reguł. Wprowadzenie zasad funkcjonowania organizacji opartych na 5S nie wymaga długiego czasu, a może dać olbrzymie korzyści. Wiele drobnych usprawnień przyczynić się może do osiągnięcia dobrego wyniku w przyszłości. Praktyki te są wstępem do uzyskania większej produktywności, pozwalają wprowadzić i wdrożyć z powodzeniem inne metody czy systemy, jak TPM, JiT, SMED czy ISO.
Nazwa 5S pochodzi od japońskich określeń rozpoczynających się od litery s (seiri, seiton, seiso, seiketsu, shitsuke). Wszystkie elementy tworzą całość, przy czym proces wdrażania wymaga zachowania kolejności poszczególnych elementów (rysunek). Jeżeli przedsiębiorstwo będzie odbiegało od metodyki wprowadzania, od zasad postępowania, to niestety system ten może spotkać się z porażką. Zachowana odpowiednia kolejność wymusza w pewien sposób „odchudzanie”, a następnie utrzymanie w czystości i sprawności miejsca pracy. Takie działanie w konsekwencji pozwala stworzyć odpowiednie warunki do wszelkich usprawnień techniczno-organizacyjnych (Kaizen).
Trzy pierwsze S służą przede wszystkim wprowadzeniu, zaś kolejne utrzymywaniu i poprawianiu obowiązujących standardów na lepsze według filozofii ciągłego doskonalenia – Kaizen. Kolejne słowa oznaczają:
- seiri – selekcja – oddzielenie potrzebnych narzędzi, przyrządów, części i instrukcji w codziennej pracy od tych, które są niepotrzebne i usunięcie ze stanowiska pracy oraz otoczenia rzeczy niepotrzebnych i nieużywanych;
- seiton (systematyka) – porządkowanie rzeczy pozostałych po serii, polega m.in. na odpowiednim oznakowaniu oraz umieszczeniu zgodnie z zasadą „właściwe rzeczy, we właściwym miejscu i we właściwym czasie”; należy rzeczy ułożyć tak, aby zminimalizować czas i wysiłek szukania;
- seiso (sprzątanie) – porządkowanie i utrzymywanie stanowiska pracy i jego otoczenia w czystości;
- seiketsu (standaryzacja) – częste stosowanie, nawet codziennie seiri, seiton i seiso, w celu utrzymania idealnych warunków w miejscu pracy, utrzymywanie czystego i zdrowego środowiska pracy, wprowadzenie zrozumiałych standardów i procedur; przedstawienie wyników działań, np. w formie wizualizacji;
- shitsuke (samodyscyplina, samodoskonalenie) – oznacza budowanie i utrzymywanie samodyscypliny przez stosowanie się do obowiązujących norm, zarządzeń, przestrzeganie 5S i dążenie do ciągłego ich doskonalenia.
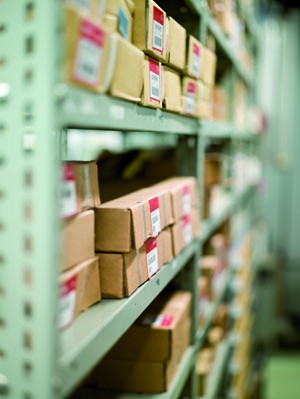
Aby 5S jako metoda usprawnienia działań nieustannego doskonalenia mogła funkcjonować, cała firma powinna wiedzieć, jakie korzyści może przynieść 5S dla pracownika i organizacji. Każdy pracownik od najniższego do najwyższego szczebla powinien być świadomy wdrażania, znać podstawowe zasady, a także przejść odpowiednie szkolenia. Ponadto ważna jest świadomość możliwości pojawiania się w działalności różnych rodzajów marnotrawstwa, prowadzących do błędów i defektów, a w konsekwencji do kosztów. Można wskazać, jak praktyki 5S mogą zapobiec ich powstawaniu.
Najważniejsze źródła marnotrawstwa i towarzyszące im błędy w organizacji czy usterki to m.in.:
- niepotrzebny zapas, który prowadzi do dodatkowych kosztów związanych z magazynowaniem, zarządzaniem zapasami, dodatkowymi pracownikami obsługującymi gospodarkę magazynową;
- niepotrzebne dokumenty i materiały wymagające dodatkowej powierzchni magazynowej i półek;
- coraz więcej półek, szafek itp. jest potrzebne tylko po to, aby przechowywać zbędne przedmioty;
- niepotrzebny transport wymaga dodatkowych palet i wózków;
- sortowanie większych ilości wymaganych produktów staje się coraz trudniejsze, z przedmiotów potrzebnych do niepotrzebnych;
- coraz większe ilości przechowywanych produktów ulegają procesowi starzenia się ze względu na nowe wzornictwo, projekty, upłynięcie terminu przydatności, skrócony czas cyklu życia produktu;
- wady jakościowe wynikają ze zbędnych zapasów w procesie i z awarii maszyn,
- niepotrzebny sprzęt utrudnia codzienną realizację działań produkcyjnych;
- obecność niepotrzebnych przedmiotów utrudnia właściwe rozplanowanie przestrzenne sprzętu.
Przestrzeganie metody 5S w miejscu pracy gwarantuje m.in.: redukcję kosztów poprzez eliminację wszelkiego marnotrawstwa, zbędnych działań i zbędnych ruchów. Zapobiega też powstawaniu strat i ubytków. Prowadzi do ułatwienia pracy poprzez precyzowanie instrukcji pracy, redukuje opóźnienia. Zapewnia lepszą, stałą, a nawet wysoką jakość, większą wydajność zarówno pracowników, jak i maszyn, wyższy poziom bezpieczeństwa i higieny pracy poprzez eliminowanie awarii i wypadków przy pracy. 5S poprawia samopoczucie pracowników, promuje dobre kontakty między pracownikami różnych działów, a co najważniejsze daje niezbędne podstawy do dalszego doskonalenia jakości. Ponadto poprzez wprowadzenie zasad wpływa także na satysfakcję klienta.
Ale mimo tak wielu korzyści, metoda ta spotyka się niestety w wielu przedsiębiorstwach z oporem ze strony zarówno kierownictwa, jak i pracowników z produkcji, magazynu czy biura. Skutkuje to niestety niepowodzeniem i brakiem motywacji do wdrożenia 5S, najczęściej w początkowej fazie czy jej kontynuowania w czasie późniejszym. Jeżeli wszelkie opory zostaną zignorowane, a praktyki mimo tego będą wprowadzane, to niestety rezultaty mogą się okazać jedynie powierzchownymi usprawnieniami. Najczęściej wyrazem postawy oporu są formułowane pytania:
- Co jest takiego specjalnego w selekcji i systematyce? – ten bezpośredni opór wobec 5S jest jak pytanie „po co robić tyle szumu o coś tak oczywistego”? Ten opór wynika z poczucia upokorzenia, kiedy ludziom wydaje się, że są traktowani jak dzieci. Kluczem do sukcesu przed wdrożeniem 5S jest wyeliminowanie poczucia upokorzenia.
- Dlaczego ja Prezes mam być prekursorem 5S? – najczęściej szefowie firm uważają, że nie muszą się angażować w tak błahe sprawy i delegują przewodnictwo na menedżera średniego szczebla. Nie wierzą, że podstawy 5S są tak ważne i nie zdają sobie sprawy, jak trudno wprowadza się 5S. Wdrożenie 5S wymaga przywództwa, a naczelne kierownictwo musi odrzucić próżne uprzedzenia i zaangażować się osobiście.
- Po co sprzątać, jeśli za chwilę znowu się pobrudzi? – pracownicy przyzwyczajają się do nieporządku, jako rzeczy nieuniknionej w ich miejscu pracy. Uznają, że sprzątanie niewiele zmieni. Postawa akceptacji braku czystości w miejscu pracy musi zostać wyeliminowana.
- Wprowadzanie selekcji i systematyki nie zwiększy produkcji – bardzo często pracownicy i ich kierownictwo oceniają produktywność poprzez ruch i pot, a w fabryce bywa, że ruch jest formą marnotrawstwa. Ważne jest, aby umieć odróżnić poruszanie się od pracowania.
- Dlaczego zajmujemy się takimi banalnymi sprawami? Po co zajmować się drobiazgami? – bardzo często opór stawiają menedżerowie średniego szczebla, np. kierownicy, liderzy czy koordynatorzy. Uznają oni, że brud to drobna sprawa i nie stanowi zbyt poważnego problemu. Menedżerowie którzy zaniedbują tę sprawę najczęściej kończą z niezdyscyplinowaną załogą. Należy eliminować niechęć i brak poparcia menedżerów dla 5S.
- My już wprowadziliśmy selekcję i systematykę – niektórzy menedżerowie dostrzegają tylko powierzchowne i widoczne gołym okiem aspekty 5S. Myślą, że odkładanie wszystkiego na swoje miejsce wystarczy. Ładne rozmieszczenie przedmiotów i generalne odświeżenie to typowe zachowanie przed przyjazdem gości czy wizytacją lub kontrolą. Takie działania tylko zahaczają o powierzchnię tego, o co chodzi naprawdę w 5S.
- Moje dokumenty to jeden wielki bałagan – ale ja zawsze wiem, gdzie co jest! – niektórzy są w stanie pracować pomiędzy stosami dokumentów, ale nie widzą przełożenia tego stanu na wydajność. Są przeciwni ingerencji w wygląd ich biurka, standaryzacji i wdrażaniu 5S. Należy przede wszystkim wprowadzić standaryzację w działania pracowników i umożliwić dostęp do dokumentów wszystkim, którzy tego potrzebują.
- Wprowadzaliśmy 5S wiele lat temu – ten komentarz obrazuje niezrozumienie idei 5S. Skoro wprowadzono to 20 lat wcześniej, po co zawracać sobie tym głowę teraz – takie podejście jest mylne. 5S nie jest przemijającą modą. Jest gruntem do wprowadzania usprawnień i podstawą długofalowego rozwoju.
- 5S i związane z nimi usprawnienia dotyczą tylko fabryki i produkcji – w niektórych firmach pracownicy związani z produkcją energicznie angażują się w proces wdrażania 5S, podczas gdy pracownicy biurowi czy sprzedaży twierdzą, że to nie ma z nimi nic wspólnego. Nie widzą związku pomiędzy bałaganem w biurze, a brudem na linii produkcyjnej. Dlatego wdrożenie 5S musi być programem obejmującym całą firmę.
- Jesteśmy zbyt zajęci, żeby tracić czas na selekcję i systematykę – na niektórych stanowiskach pracy selekcja i systematyka to pierwsze rzeczy do zignorowania, kiedy robi się naprawdę „gorąco”. Za chwilę wszystko leży porozrzucane dookoła. Wytłumaczenie jest zawsze to samo „jesteśmy zbyt zajęci”. Tak naprawdę pokazują swoje prawdziwe podejście, mówiąc „nie mamy czasu na porządki i sprzątanie”, i to jest ich wymówka.
- Kim oni są, żeby mówić mi, co mam robić? – często na początku wdrożenia 5S zderzają się z problemami relacji międzyludzkich. Dochodzi do sytuacji, gdzie osoba rozumiejąca wagę praktyk 5S sprzeciwia się poleceniom wydawanym przez specjalnie powołany zespół do wdrożenia 5S. Warto więc sformować zespoły 5S z osób obdarzonych zdolnościami interpersonalnymi.
- Niepotrzebne nam 5S – my robimy pieniądze, więc dajcie nam robić to, co trzeba! – czasami trudno jest wprowadzać 5S lub inny usprawniający program w organizacji, która jest obecnie rentowna. Próbując wprowadzać efektywne rozwiązanie, można napotkać opór w postaci „dobrze nam idzie i chcemy żeby tak zostało”. Należy spojrzeć kompleksowo na przepływy w produkcji, podczas gdy pracownicy patrzą raczej na indywidualne procesy. Niewłaściwy rytm produkcji skupiony na rezultatach poszczególnych stanowisk prowadzi do strat czasu. W długim okresie takie podejście jest szkodliwe dla firmy.
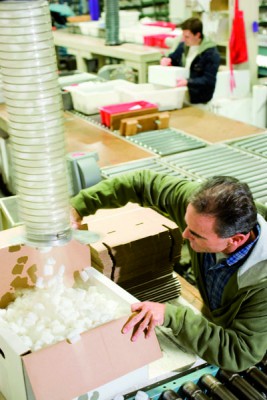
Zatem do najczęstszych przyczyn niepowodzeń zastosowania praktyk 5S można zaliczyć: obawę przed zmianami przyzwyczajeń, opór ze strony pracowników, brak zaangażowania wszystkich szczebli zarządzania, brak szkoleń z zakresu 5S, nieświadomość i niewłaściwe podejście pracowników dotyczące podstawowych etapów, zbyt wczesne przerwanie wdrażania, brak konsekwencji, realizowanie tylko wybranych etapów metody, niezrealizowanie w pełnym wymiarze wyznaczonych zasad, a tylko wybrane elementy, niejasne, mało czytelne procedury i standardy, brak cierpliwości w osiąganiu wyników czy zbyt wysokie oczekiwania co do osiągnięcia pozytywnych wyników w krótkim czasie.
W drugiej części artykułu opisane zostaną: etapy postępowania przy wprowadzaniu kolejnych S, środowiska zastosowań oraz efekty, jakie metoda 5S przynosi organizacji.
dr Agnieszka Piasecka-Głuszak
Katedra Międzynarodowych Stosunków Gospodarczych
Uniwersytet Ekonomiczny we Wrocławiu