Odchudzanie końca linii produkcyjnej z wykorzystaniem bezzałogowych wózków LGV.
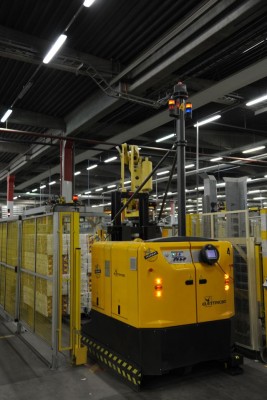
Z zakładu produkcyjnego DELITISSUE w Ciechanowie codziennie do klientów z całej Europy wyjeżdżają tysiące sztuk produktów toaletowych wykorzystywanych na co dzień w każdym gospodarstwie domowym. Papierowe ręczniki, papier toaletowy i chusteczki higieniczne popularnej marki Regina w dziesiątkach wersji kolorystycznych i zapachowych produkowane są w trybie trzyzmianowym przez siedem dni w tygodniu. Za organizację końca linii produkcyjnej, z której w trakcie jednej zmiany schodzi około tysiąca palet, odpowiada system Freeway® firmy Elettric 80 oparty o pracę bezzałogowych wózków LGV i automatycznych owijarek do palet.
Manualna przeszłość
Obecnie w zakładzie DELITISSUE pracują cztery linie produkcyjne wyrobów rolkowych (papier toaletowy i ręczniki) oraz trzy linie wyrobów składanych (chusteczki higieniczne i kosmetyczne). Przed wdrożeniem rozwiązania automatycznego konfekcjonowanie zbiorcze na końcu linii produkcyjnej odbywało się w sposób manualny. Pojedyncze opakowania z wyrobem gotowym, pakowane po osiem lub po cztery rolki, opuszczały strefę maszyn pakujących i układane były na palecie ręcznie przez operatorów dedykowanych do obsługi poszczególnych gałązek pakujących. Następnie skompletowane palety operator odstawiał wózkiem paletowym na pole odkładcze, z którego wózek widłowy transportował je na owijarkę i po zabezpieczeniu składowane były w stosach, oczekując na odbiór i umieszczenie w magazynie wyrobów gotowych. Taka organizacja pracy przysparzała sporo problemów związanych ze sprawnym przepływem pomiędzy strefą pakowania a magazynem wyrobów gotowych.
Ówczesne rozwiązanie oznaczało, że w strefie konfekcjonowania zbiorczego przebywało jednocześnie kilkanaście osób, co powodowało częste problemy komunikacyjne z operatorem wózka widłowego. Te z kolei wpływały na czas oczekiwania na odebranie skompletowanych palet ze strefy i niepotrzebne przestoje. Ponadto ręczne układanie opakowań na palecie nie było na tyle precyzyjne, aby zapewnić stuprocentową powtarzalność ułożenia pojedynczych sztuk w stosie. Wbrew pozorom jest to ważne, ponieważ niewielkie nawisy na pojedynczej palecie przekładają się na problemy ze stabilnością ładunku składowanego w stosie, a z takim składowaniem mają do czynienia pracownicy magazynu wyrobów gotowych.
Niezbędna reorganizacja
Wdrożenie automatycznego systemu końca linii produkcyjnej ruszyło w 2003 r. Proces okazał się dużym wyzwaniem zarówno dla kierownictwa fabryki, jak i dla pracowników firmy Elettric 80. Projekt wiązał się z koniecznością przebudowania strefy w kilku newralgicznych punktach, począwszy od maszyn pakujących, z których pierwotnie opakowania z wyrobem gotowym operatorzy odbierali ręcznie. Maszyny pakujące zostały zatem zaopatrzone w system transportu rolkowego, który na wyjściu odbiera od nich opakowanie i przemieszcza automatycznie do punktu, z którego robot paletyzujący przejmuje opakowania i ze stuprocentową precyzją układa na palecie. Dla zapewnienia stabilności ładunku układanego w wysokie stosy robot paletyzujący co kilka warstw układa specjalnie do tego celu przygotowane przekładki antypoślizgowe. Takich robotów marki Fanuc, na końcu linii pracuje obecnie dziesięć. Po skompletowaniu palety z towarem trafia ona w wydzielone miejsce przy każdym stanowisku, z którego następnie odbierana jest przez automatyczny wózek LGV (Laser Guided Vehicle). Zastąpienie człowieka w realizacji tego zadania nie oznaczało całkowitej eliminacji osób wcześniej odpowiedzialnych za ten proces. Zgodnie z duchem Lean pracownicy zostali przeniesieni w inne miejsce na linii produkcyjnej, w której siła robocza była bardziej potrzebna, aniżeli w strefie wyjścia. W niej na każdej zmianie pracuje dziś tylko jedna osoba, której zadaniem jest nadzór nad prawidłowym funkcjonowaniem wszystkich urządzeń, czyli manipulatorów, wózków LGV i owijarek (wymiana rolek folii, reagowanie na ewentualne zacięcia itp.).
Wózki w roli operatorów
Zorganizowanie strefy transportu za pomocą urządzeń LGV również stanowiło duże wyzwanie dla obu stron. Kluczowym aspektem dla zapewnienia efektywnej pracy bezzałogowych wózków LGV było dostosowanie posadzki do pracy tych pojazdów, bowiem wymagają one bezwzględnej równości w celu zminimalizowania prawdopodobieństwa wystąpienia jakichkolwiek drgań i wibracji podczas ich przemieszczania się. Koła takich wózków i wykorzystywana w sterowaniu nimi elektronika są bowiem bardzo wrażliwe na wszelkie drgania, dlatego nawet najdrobniejsze odchylenia od normy powstające przy posadzce przekładają się na możliwość wystąpienia dużych wahań masztu. Na nim zlokalizowane są nadajniki i odbiorniki odpowiedzialne za skanowanie luster i wysyłanie sygnału do detektorów, czyli bezpośrednie sterowanie wózkami. Wyzwaniem dla inżynierów Elettric 80 było natomiast precyzyjne wytyczenie tras i węzłów komunikacyjnych, po których wózki będą się poruszać, punktów, z których będą odbierać palety i do których będą je zawozić. W praktyce przemieszczają się one po dwóch liniach, obsługując dziesięć stanowisk paletyzujących automatycznie oraz jedno dodatkowe, na które operator może ręcznie dostarczyć paletę i przywołać wózek w celu jej odbioru, przyciskając odpowiedni przycisk na stanowisku. Po odebraniu palety, wózki LGV przemieszczają je każdorazowo na jedną z trzech pracujących obecnie na samym końcu linii owijarek, które zabezpieczają paletę z wyrobem gotowym przed wydaniem jej do magazynu.
Obserwując pracę wózków poruszających się po wytyczonych trasach, można odnieść wrażenie, jakby „znały się one od lat”. Dosłownie i w przenośni można powiedzieć, że pojazdy te „rozumieją się bez słów”, gdyż zapamiętując trasy, po których się poruszają, zadania, które mają do wykonania i punkty, z których będą odbierać poszczególne palety, wózki LGV mijają się na linii ze zdumiewającą precyzją. System planuje dla nich trasy w taki sposób, aby zapewnić maksymalną sprawność przepływu bez możliwości dopuszczenia do kolizji. Należy zaznaczyć, że bezbłędne sterowanie wózkami nie funkcjonowało od zaraz. Proces dostrajania i wprowadzania wszelkich modyfikacji w celu osiągnięcia optymalnego poziomu obsługi zajął inżynierom fabryki i firmy Elettric 80 około roku i jest de facto procesem ciągłym. – Te zadania związane z dostrojeniem systemu do wymagań zdefiniowanych przez przyszłego użytkownika, który przewiduje dla systemu określone możliwości, zasadniczo są częścią kontraktu. Jeżeli dochodzi do jakichś modyfikacji na etapie dalszej eksploatacji, mówimy już o obsłudze serwisowej – mówi Tomasz Siepetowski z firmy Elettric 80.
Wyposażone w systemy identyfikacji wszystkich fizycznych przeszkód na swojej trasie, wózki stanowią wyjątkowo bezpieczne rozwiązanie. Manipulując ładunkiem, wykonują na trasie szereg zwrotów w różnych kierunkach. System sterowania wózkami na trasie jest zaprojektowany w taki sposób, że planuje takie odległości podczas wykonywania operacji, iż wzajemne mijanie się wózka nie wymaga nawet zwolnienia prędkości. Takie wyhamowanie ma miejsce jedynie wówczas, kiedy w strefie pojawi się inna przeszkoda, np. człowiek. W takiej sytuacji, przemieszczając się obok przeszkody, pojazd zwalnia, a w momencie, gdy „wie” już, że nie będzie w stanie samodzielnie ominąć przeszkody, zatrzymuje się. Na wszelki wypadek każdy z czterech pracujących w tej strefie wózków wyposażony jest w przyciski typu andon służące do ich zatrzymania. Zlokalizowane z każdej strony pojazdu tak, aby w sytuacji zagrożenia przynajmniej jeden zawsze był w zasięgu ręki zagrożonego.
Bezpieczeństwo i bezkolizyjność pracy wózków LGV wpływa znacząco na ich bezawaryjność. W prawie dziesięcioletniej historii ich pracy w zakładzie DELITISSUE zarządzający fabryką nie spotkali się z większymi problemami związanymi z technicznym funkcjonowaniem urządzeń. Jednak nawet, w sytuacji zaistnienia jakiejkolwiek usterki technicznej, ewentualny problem nie wpływa znacząco na ciągłość procesu. Wózki zaopatrzone są w panel sterujący, który uruchamia się w wypadku awarii i za pomocą joysticka odholowuje się go poza strefę. Obsługą palet zajmują się w tym czasie pozostałe pojazdy, a w razie potrzeby możliwy jest wjazd tradycyjnego wózka widłowego. Po usunięciu awarii wózek jest resetowany, wraca do strefy i kontynuuje realizację przypisanych mu zadań.
Michał Klecha