Nie nadążamy za resztą świata w zastosowaniu przemysłowych robotów. Nie chodzi nawet o to, że jesteśmy w tyle, lecz nie wykazujemy chęci wprowadzania tych innowacji. Tym bardziej, że finansowa bariera do zakupu tych maszyn wyraźnie stopniała. Wciąż jednak posiłkujemy się mitami, które przykrywają rzeczywiste korzyści, płynące z zastosowania robotów.
Na automacie
Z niechęcią do robotów wśród polskich przemysłowców jest trochę jak z brakiem przekonania kierowców do samochodów z automatyczną skrzynią biegów: niby wygodne, ale istnieje ryzyko awarii, a w dodatku auto z punktu pali więcej. Te społeczne mity już dawno zostały obalone. Jednak kiedy większość ludzi w państwach Zachodu wybiera samochód z automatem, w naszym kraju nadal najwięcej mamy zwolenników tradycyjnych rozwiązań, chociaż innowacyjne przekładnie w samochodach mają stałą grupę amatorów. Podobnie z robotyzacją. Wszystkie twarde dane wskazują, że rośnie liczba robotów świecie. Wskazuje na to najnowszy raport Międzynarodowej Federacji Robotyki „Roboty przemysłowe 2015” (czytaj „Kaizen” 5/2016, artykuł pt. „Świat autonomicznych maszyn”), który przynosi informacje o globalnej sprzedaży robotów przemysłowych w liczbie 257 748, co oznacza 15 proc. więcej sprzedanych urządzeń niż w roku poprzednim. Dla porównania, jak wskazuje raport, w Polsce w tym czasie w branży przemysłowej zaimplementowano 1795 urządzeń. Łącznie mamy nieco ponad 8 tys. robotów, co oznacza wzrost o 27 proc. w porównaniu do roku 2014. Obserwuje się tendencję wzrostową, ponieważ od 2009 r. przyrost inwestycji z udziałem robotów jest ponadtrzykrotny. W zestawieniu jednak z liderami wdrożeń zainteresowanie robotyką wykazuje mała liczba śmiałków.
Doskok do czołówki
Poszukiwanie przyczyn niskiej dynamiki inwestycji w roboty przemysłowe skorelowane jest z zasadniczym pytaniem o innowacyjność rodzimej gospodarki. Z danych, jakie przynosi najnowszy raport Organizacji Współpracy Gospodarczej i Rozwoju (OECD), dotyczący wydatków ponad 40 krajów na badania i rozwój, wynika, że jesteśmy na 35. miejscu zestawienia. Wydaliśmy jako państwo w 2014 r. niespełna 1 proc. swojego PKB na szeroko rozumiane innowacje, co oznacza równowartość 234 dolarów na statystycznego Kowalskiego. Za nami znalazły się: Grecja Argentyna, RPA, Meksyk, Chile i Rumunia. W krajach Europy Wschodniej więcej od nas wydają np. Węgrzy, przeznaczający 1,4 proc. swojego PKB. Liderami wydatków na innowację są: Korea Południowa – 4,3 proc., Izrael – 4,1 proc. czy Japonia – 3,6 proc. Nasze wydatki są zdecydowanie mniejsze także na tle OECD i UE, gdzie na programy innowacyjne wydaje się odpowiednio 2,4 proc i 1,9 proc. PKB.
Dlaczego tak się dzieje i nie jesteśmy skorzy wydawać pieniędzy, aby doskonalić fabryki i gospodarkę? Analitycy podkreślają, że stoi za tym opór mentalny. Jak długo nie musimy z nikim konkurować, a możemy czerpać zyski w dotychczasowej formie, nie potrafimy się przełamać. Słowem, po co inwestować, skoro starcza nam to, co mamy. Jak zatem gonić świat, który coraz szybciej ucieka, a proste przewagi konkurencyjne, jak choćby tania siła robocza, są na wyczerpaniu?
Mity, lęki, fobie
Ironicznie podchodząc do sprawy, przydałaby się kuracja psychoanalityczna, aby pozbawić nas mitów, leków i fobii. Nie bez kozery o tym piszę, ponieważ badania ankietowe Instytutu Badań nad Gospodarką Rynkową, wykonane przy współpracy z FANUC Polska, pod nazwą „Wpływ robotyzacji na konkurencyjność polskich przedsiębiorstw” ujawniły kilka interesujących argumentów na „Nie” wobec robotyzacji. W tym przypadku przedsiębiorcy, którzy do tej pory nie dokonali żadnych inwestycji w dziedzinę maszyn inteligentnych, ujawniają opinie oparte o własne przemyślenia i doświadczenia produkcyjne. Po pierwsze, w 71 proc. przypadków ankietowani wskazują, że ich profil działalności i produkty, które wytwarzają, nie wymagają wsparcia ze strony robotów. Po drugie, są zbyt małymi organizacjami, których produkcja ma ograniczony popyt, toteż 37 proc. z nich uważa, że nie wykorzystałoby robotów w pełni, a co za tym idzie – inwestycja nie miałaby ekonomicznego uzasadnienia. Po trzecie, chyba najciekawsze z punktu widzenia mitów – aż 34 proc. z nich zakłada z góry, że robotyzacja nie przyniesie firmie dodatkowych korzyści ekonomicznych. Warto rozwinąć ten argument, który używany jest w kontrze do wzrostu produktywności, redukcji kosztów, poprawy konkurencyjności, najczęściej wskazywanych przez organizacje inwestujące w robotyzację, jako efekt pozytywnych zmian. I jak to z mitami często bywa, nie jest oparty o jakiekolwiek dane analityczne. W tej walce z ograniczeniami świadomości lepsza niż kozetka psychoanalityka powinna okazać się rzetelna informacja i edukacja. W końcu po czwarte, 23 proc. przedsiębiorców nie widzi potrzeby robotyzacji, ponieważ uważa, że ich proces technologiczny jest odpowiedni i nie wymaga doskonalenia i wprowadzania innowacji. Tym samym lekceważy się koronny argument zwolenników wprowadzania automatyzacji produkcji, mówiący o zwiększaniu konkurencyjności firmy, która zależy od technologii.
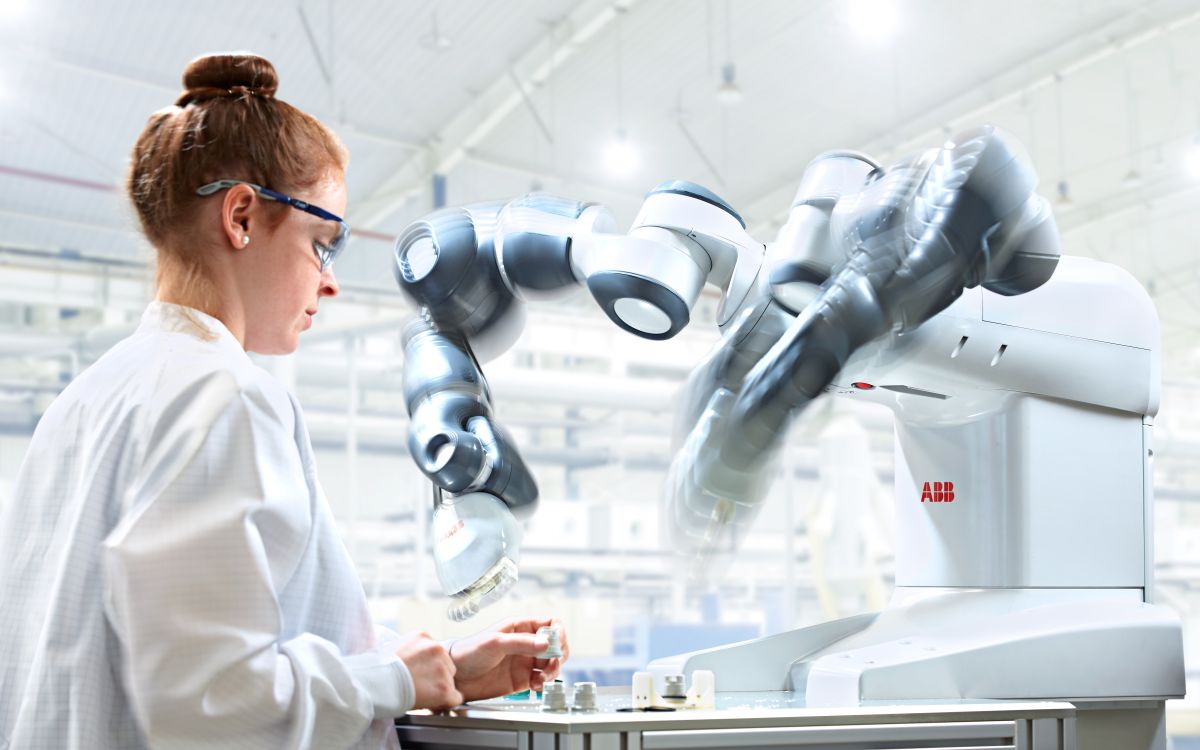
ABB
Kasa, kasa, kasa
Osobny wątek należy się barierom finansowym. W argumentacji negatywnej, która powstrzymuje inwestycje, pieniądze i ich brak stanowią 13 proc. odpowiedzi. Zatem nie jest to najważniejsza bariera uniemożliwiająca zakup robotów, o której najczęściej mówi się na pierwszym miejscu przy okazji rozmów o przyczynach niskiej dynamiki robotyzacji w kraju. Roboty są w zasięgu ręki naszych firm, ponieważ ich ceny obecnie zaczynają się od 15–20 tys. euro. Oczywiście na ostateczne koszty składa się nie tylko zakup maszyny, ale dodatkowo oprzyrządowania roboczego w postaci np. dedykowanego chwytaka, który trzeba wykonać na indywidualne zamówienie. Do kosztów wdrożenia należy dodać proces przyuczania maszyny do pracy, czyli mapę ustawień, a także – wbrew mitom – wzrost zatrudnienia. Zatrudnienie wcale może nie spaść, lecz powiększyć się za sprawą choćby nowej ekipy SUR. Suma wydatków może zawędrować w wypadku skomplikowanego robota nawet do wysokości kilkuset tysięcy euro. Ważna uwaga: tak samo jak wartość maszyny, istotny jest jej pay back. Obecnie spadł on znacząco i w wariantach maksymalnego wykorzystania maszyny może trwać mniej niż rok. Z reguły zwraca się ona w okresie 2–3 lat od chwili zakupu.
Polska i reszta świata
Raport „Roboty przemysłowe” przynosi dane porównawcze na temat wskaźnika gęstości robotyzacji. Jest to parametr określający liczbę robotów przypadających na 10 tys. pracowników zatrudnionych w przemyśle. We wspomnianej wcześniej Korei Południowej nakłady na innowacje znajdują odbicie w gęstości robotyzacji, której wskaźnik wynosi 531 sztuk. Tym samym Korea należy do najbardziej zautomatyzowanych krajów na świecie. W Europie prymat pod tym względem należy do Niemiec – 301. W Polsce wskaźnik gęstości robotyzacji plasuje się średnio na poziomie 28 maszyn i zdaniem autorów analizy w porównaniu do krajów regionu wciąg wypadamy najgorzej. Lepsi są od nas Czesi – 93, Słowacy – 79 i Węgrzy – 57, a wszystkie te wartości oscylują wokół wartości uznawanej na świecie za średnią, czyli 69 robotów przypadających na 10 tys. pracowników.
Megatrendy wyznaczają duże organizacje koncernowe. Nie inaczej jest w przypadku automatyzacji produkcji i związanych z nią nowych technologii, które uznawane są z punktu jako rynkowa przewaga konkurencyjna. Zwykle chodzi o osiągnie najwyższej jakości produktu, powtarzalności i wydajności, co jest niemożliwe do spełnienia bez wysokiej technologii. Za taką wymagającą branżę uznaje się motoryzację i tam też implementuje się najwięcej robotów. Nieprzypadkowo to właśnie sektor automotive nadaje rytm tym wdrożeniom, co odbija się we wskaźniku gęstości robotyzacji, który wynosi 131 jednostek. Dla porównania, średnia dla sektora produkcji wynosi 28 robotów. Poza motoryzacją statystykę wdrożeń podbija przemysł metalowy, chemiczny oraz spożywczy, korzystające z robotów zwykle tam, gdzie funkcjonują procesy spawania, paletyzacji i stanowiska pracy, wymagające podawania i manipulacji produktem.
Efekt robota?
Odpowiedź nie jest jednoznaczna i warto poznać argumenty, które używane są w dyskusji na „Tak” za robotyzacją. Wróćmy zatem do analiz przygotowanych przez Instytut Badań nad Gospodarką Rynkową, który dostrzegł w ankietach cztery grupy efektów z wprowadzenia robotyzacji: finansowe, rynkowe, produkcyjne i efekty dla pracowników.
W przypadku pierwszej grupy na czoło wysuwają się opinie, że zastosowanie robotów pozwoliło odnotować wzrost produkcji, co przyznaje 84 proc. badanych. Blisko 80 proc. firm, które zainwestowały w roboty, odnotowało spadek kosztów produkcji. To wynik spadku jednostkowego kosztu wytworzenia wyrobu z powodu m.in. szybszej produkcji. W efekcie 58 proc. badanych dostrzegło poprawę rentowności i sytuacji finansowej organizacji.
Efekty rynkowe stanowią drugi zauważalny element inwestycji w automatyzację linii technologicznej. Ankietowani są zgodni w stu procentach, że robotyzacja prowadzi do poprawy konkurencyjności przedsiębiorstwa. Wzrost mocy produkcyjnych, niższe koszty wytwarzania oraz poprawa jakości wyrobów są głównymi czynnikami poprawiającymi pozycję konkurencyjną firm, które wdrożyły w swoich zakładach roboty przemysłowe. Tym samym 68 proc. badanych uznało robotyzację za narzędzie kreowania popytu rynkowego produktów, poprzez zachowanie nienagannej jakości i atrakcyjnej ceny.
Robotyzacja zmienia organizację pracy fabryk i samych produktów, co należy zaliczyć do efektów produkcyjnych inwestycji w nowe technologie. Zdaniem 84 proc. ankietowanych chodzi o większe zaawansowanie technologiczne wyrobów, jakie stało się efektem wdrożenia robotów. A 58 proc. z uczestników ankiety wskazało jako efekt zmiany elastyczność – łatwiejsze przestawianie linii produkcyjnych do zmiennej produkcji, która odpowiada preferencjom odbiorców.
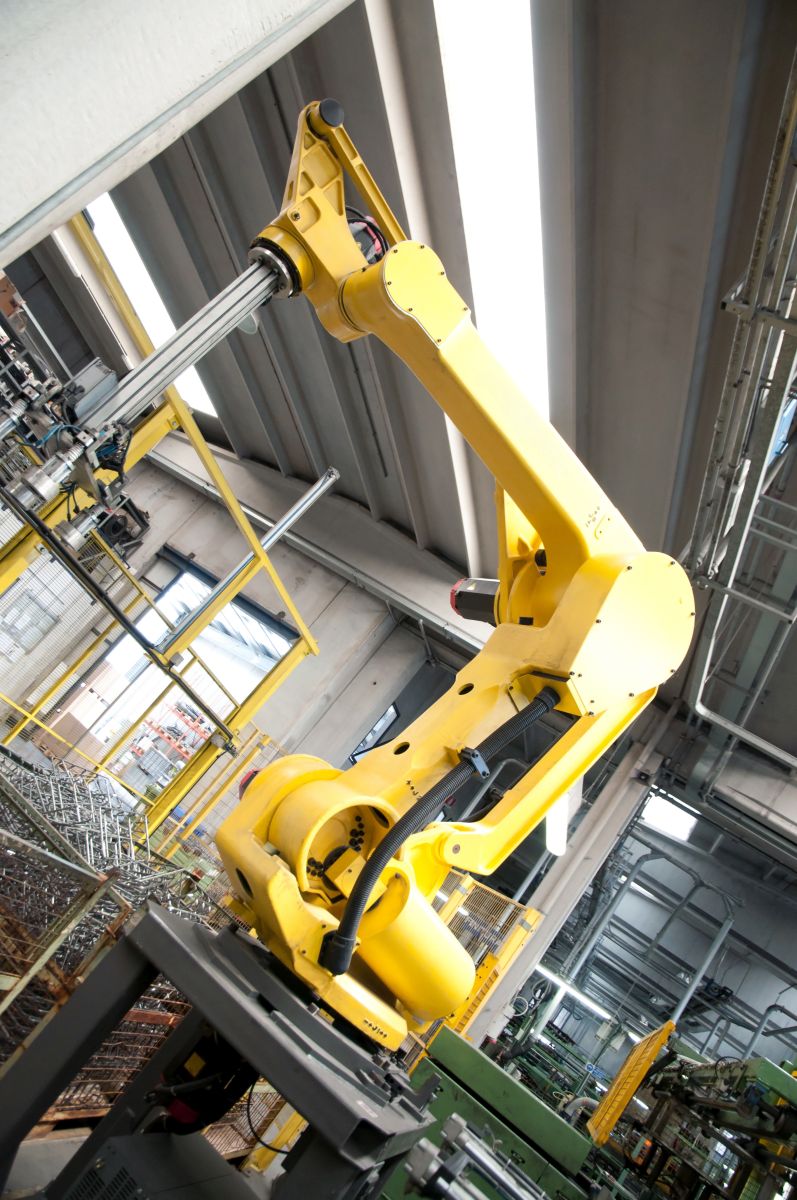
Fotolia
Od czasów pierwszej rewolucji przemysłowej poglądy, że maszyny odbierają pracę ludziom, wciąż są żywe. Nie inaczej jest w przypadku automatyzacji miejsc pracy, gdzie dotąd dominowała siła ludzkich rąk. Aspekt społeczny wprowadzanych zmian dla przedsiębiorcy i załogi może być równie trudny. Dlatego warto przyjrzeć się efektom dla pracowników, jakie dostrzega się przy okazji innowacji wprowadzanych na liniach fabrycznych. Przede wszystkim, dotychczasowi pracownicy nie zostali zwolnieni, a robotyzacja nie zmieniła poziomu zatrudnienia – mówi tak 63 proc. ankietowanych. Ale największą zaletą wdrożenia maszyn stało się podniesienie kwalifikacji zawodowych kadry pracowniczej. Aż 80 proc. ankietowanych potwierdziło ten fakt, uznając go jednocześnie za naturalną konsekwencję wprowadzenia zaawansowanych urządzeń w przedsiębiorstwie.
Dane są niepodważalne – jesteśmy obecnie najsłabiej zrobotyzowanym krajem w świecie. Demografia podpowiada nam, że liczba nowych rąk do pracy zmniejsza się z roku na rok, a spadek liczby aktywnych zawodowo pracowników to kwestia czasu. Wcale niezbyt długiego, skoro ponownie będziemy wszyscy pracować krócej z powodu nowych regulacji w sprawie wieku emerytalnego. Druga ważna informacja płynie z prognoz Międzynarodowej Federacji Robotyki, które mówią, że proces robotyzacji produkcji w Europie i na świecie przyspiesza coraz bardziej. Tylko w ciągu 2015 r. liczba robotów zwiększyła się w skali globu o 11 proc. Siłą rzeczy zwiększy się również w Polsce. O wiele łatwiej będzie jednak podejmować decyzje inwestycyjne, kierując się twardymi liczbami, aniżeli przyjmując coś na czucie i wiarę.
Krzysztof Pograniczny